Drain cleaning equipment is essential for maintaining the smooth operation of sewer, water, and wastewater systems. Whether you’re responsible for municipal services or managing facility drainage, ensuring your equipment is well maintained is critical to avoid unexpected disruptions. Poor upkeep can lead to decreased performance, frequent breakdowns, and expensive repairs—all of which escalate operating costs and cause downtime.
By following practical maintenance tips and best practices, you can minimize downtime, boost efficiency, and protect your investment in essential machinery.
The Importance of Proper Maintenance
Keeping drain cleaning equipment in optimal condition is the cornerstone of efficient and effective wastewater management. Equipment like sewer jetters, hydro excavation equipment, and inspection cameras endure heavy use in harsh environments—making regular maintenance essential for consistent performance. Well-maintained tools not only perform better; they also help save money, improve safety, and reduce the risk of unpredictable failures.
Key Benefits of Regular Maintenance
- Longer Equipment Lifespan: Routine care such as cleaning, lubricating, and inspecting for wear helps ensure critical components last longer. This practice prevents small issues—like worn seals or clogged nozzles—from escalating into costly system failures.
- Reduced Downtime: Preventive maintenance minimizes the likelihood of unexpected breakdowns, keeping your operations running smoothly even during busy periods.
- Enhanced Efficiency: Regular servicing helps your machinery maintain optimal flow pressure and effective cleaning results.
- Lower Long-term Costs: Timely repairs and the use of suitable components can reduce overall operating expenses.
- Improved Safety: Proper maintenance ensures operating conditions remain safe and reduces the risk of accidents caused by malfunctioning equipment.
Risks of Neglected Maintenance
If maintenance is ignored, drain cleaning equipment can develop issues that hinder operations:
- Weak or Inconsistent Pressure: Clogged nozzles, damaged hoses, or poorly maintained pumps can reduce water pressure and lead to inefficient cleaning.
- Frequent Repairs: Small faults or loose fittings often go unnoticed without periodic inspections, resulting in major failures.
- Overheating Issues: Poor lubrication or restricted airflow can lead to overheating, causing premature wear or severe system damage.
- Increased Vibration: Worn or unbalanced parts may cause excess vibration, accelerating damage to seals and other components.
Risks of Neglected Maintenance
If maintenance is ignored, drain cleaning equipment can develop issues that hinder operations:
- Weak or Inconsistent Pressure: Clogged nozzles, damaged hoses, or poorly maintained pumps can reduce water pressure and lead to inefficient cleaning.
- Frequent Repairs: Small faults or loose fittings often go unnoticed without periodic inspections, resulting in major failures.
- Overheating Issues: Poor lubrication or restricted airflow can lead to overheating, causing premature wear or severe system damage.
- Increased Vibration: Worn or unbalanced parts may cause excess vibration, accelerating damage to seals and other components.
Neglected maintenance poses significant threats not only to the equipment’s functionality but also to overall operational safety and efficiency. Failing to address minor issues promptly can escalate into major repairs, disrupting service and inflating repair costs. Prioritizing regular inspections and maintenance routines is crucial for mitigating these risks and ensuring reliable equipment performance.
Practical Maintenance Tips for Drain Cleaning Equipment
Performing routine maintenance tasks is key to maximizing equipment performance and minimizing costly repairs. Follow these actionable tips to keep your drain cleaning tools in top shape:
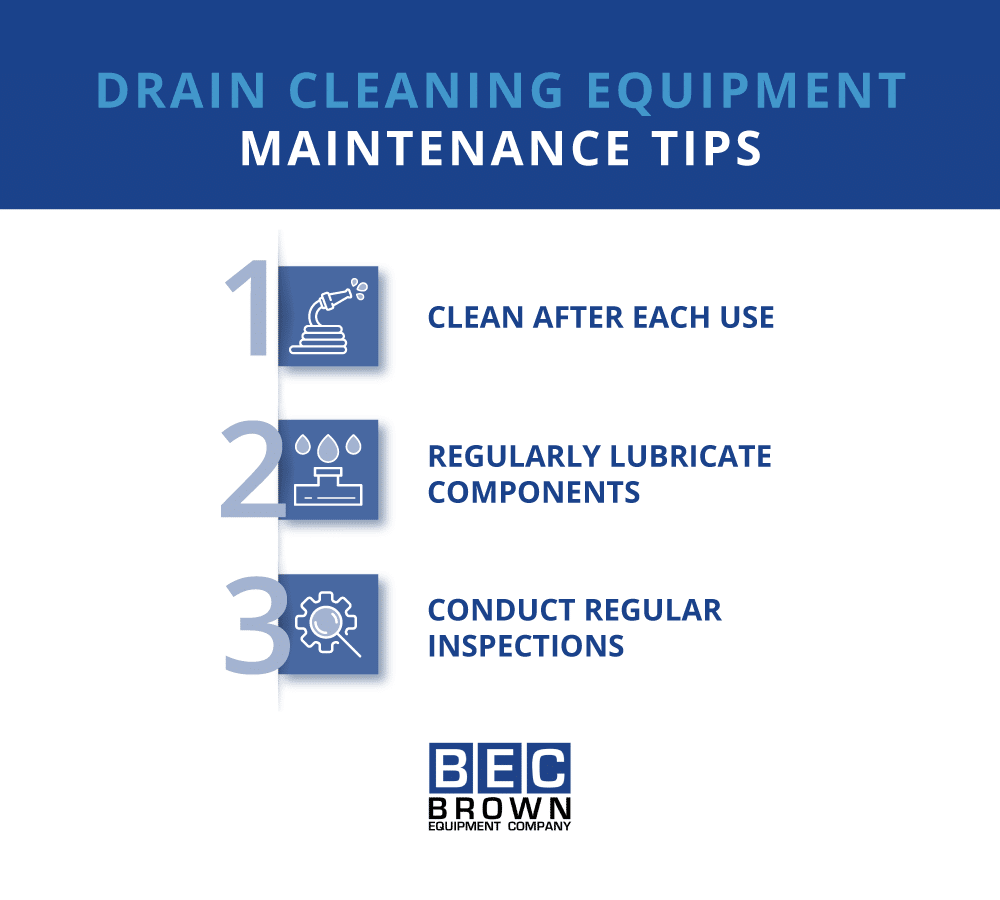
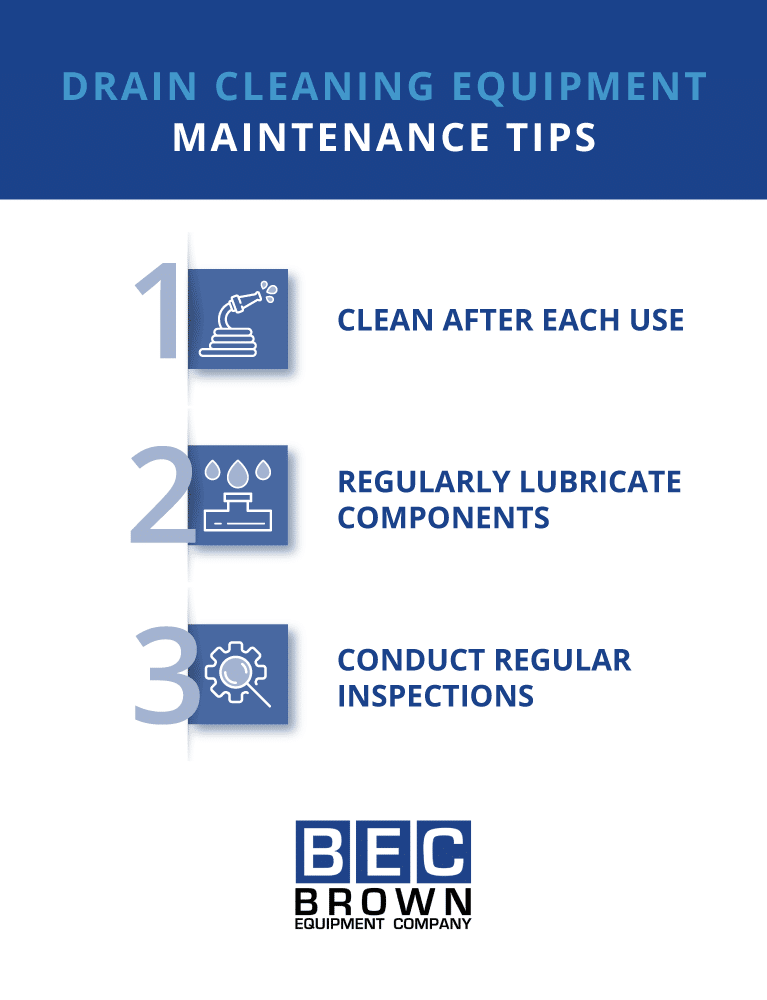
1. Clean Your Equipment After Each Use
Routine cleaning prevents debris and residue from hardening inside hoses, nozzles, and tanks.
- Flush Hoses Thoroughly: After each use, flush hoses with clean water to remove debris and ensure unrestricted flow.
- Inspect and Clean Nozzles: Residual buildup can obstruct water pressure, so rinse and clear nozzles regularly.
- Wipe Down Surfaces: Dirt on equipment surfaces can trap moisture and lead to corrosion. Use cleaning products approved by the manufacturer.
2. Regularly Lubricate Moving Components
Moving parts—like rollers, chains, and pump assemblies—require consistent lubrication.
- Use the Correct Lubricants: Follow manufacturer recommendations for best results.
- Target Key Areas: Pay special attention to fittings, pulleys, bearings, and cable drums.
- Document Lubrication Schedules: Keeping a log helps track usage patterns and potential issues.
3. Conduct Regular Inspections
Inspecting wear-prone parts regularly helps identify small problems before they escalate.
- Inspect Hoses for Damage: Look for cracks, bulging areas, or wear marks, and replace compromised hoses promptly.
- Monitor Nozzle Conditions: Replace worn or misshapen nozzles to maintain optimal water flow.
- Check Seals and Gaskets: Tight seals are crucial for high-pressure systems. Replace any seals that show signs of leaks or cracking.
Maintaining drain cleaning equipment is essential to ensuring its reliability, efficiency, and longevity. By implementing regular cleaning, lubrication, and inspection routines, you can significantly reduce the risk of equipment failure, enhance performance, and ultimately protect your investment. Prioritizing these maintenance practices not only safeguards your operations but also optimizes the effectiveness of your sewer, water, and wastewater management systems.
Preventive Maintenance Strategies to Extend Equipment Lifespan
A strong preventive maintenance strategy maximizes your drain cleaning equipment’s performance and lifespan. Beyond daily cleaning and inspections, a well-structured program addresses every component systematically for long-term reliability.
Create a Comprehensive Maintenance Checklist
A clearly defined checklist is the backbone of effective preventive maintenance.
- Focus on Key Components: Include hoses, seals, pumps, cables, lubrication points, couplings, and operator controls.
- Set Specific Timeframes: Perform maintenance tasks on weekly, monthly, or seasonal intervals.
- Provide Clear Instructions: Define acceptable wear tolerances, inspection methods, and any needed tools.
Keep a Detailed Log for Inspections and Repairs
A thorough record of maintenance activities provides insights into recurring issues.
- Track Service Dates: Detailed logs simplify warranty claims and professional service requests.
- Document Repairs: Note parts replaced, adjustments made, and any observations during maintenance.
- Record Operating Anomalies: Monitor unusual noises, leaks, or fluctuations in pressure for early detection of issues.
Plan for Seasonal Equipment Adjustments
Maintenance needs often shift with the seasons.
- Winterize Your Equipment: Prior to freezing weather, drain water from hoses and systems, and use approved antifreeze products if necessary.
- Spring Preparation: Inspect for moisture damage, stiff components, and worn belts after winter.
- Peak Season Readiness: Stock critical spare parts and increase inspection frequency during high-use periods.
Schedule Professional Inspections and Tune-Ups
Even with diligent in-house maintenance, specialized technicians can detect subtle issues.
- Leverage Advanced Tools: Techniques like pipeline camera inspections, pressure testing, and vibration analysis can uncover hidden concerns.
- Obtain Expert Recommendations: Experienced professionals can suggest upgrades, replacements, or adjustments tailored to your system’s unique demands.
Specialized Maintenance Services from Brown Equipment
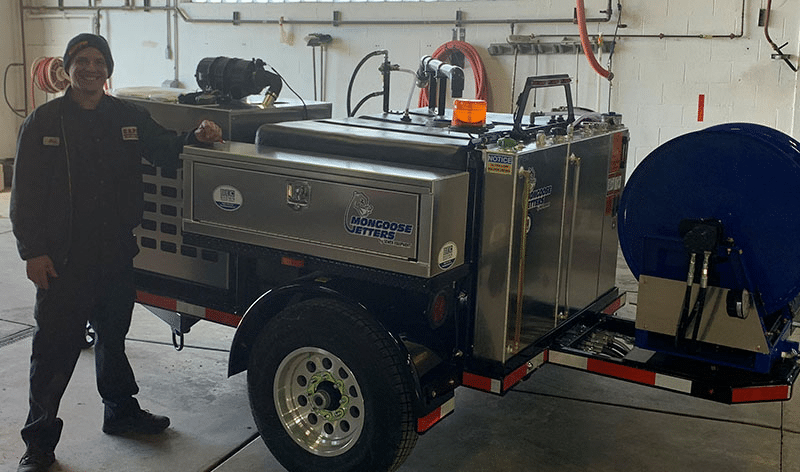
Even the most consistent in-house care can benefit from external expertise. Brown Equipment provides relationship-driven support that ranges from everyday maintenance tasks to advanced reconditioning options.
Expert Maintenance and Repairs
Brown Equipment offers extensive maintenance & repair services, addressing needs such as routine tune-ups, troubleshooting, and oversight of complex equipment issues. While highly specialized repairs may sometimes require external resources, Brown Equipment manages a wide array of common problems.
Reconditioning to Restore Performance
For aged machinery, reconditioning can be a cost-effective alternative to full replacement. Services may include rebuilding pumps, hoses, motors, or panels to restore operational integrity.
OEM Parts and Custom Fabrication Solutions
When maintaining or upgrading drain cleaning equipment, having access to Original Equipment Manufacturer (OEM) parts and custom fabrication solutions can significantly enhance operational effectiveness and efficiency. Whether it’s replacing worn components or tailoring equipment to suit specific operational needs, these services are invaluable for both performance and longevity.
Brown Equipment maintains a robust stock of genuine parts for quick replacements that meet original specifications. For unique operational demands, they offer custom fabrication.
Training and Best Practices for Equipment Operators
Well-trained operators are crucial for maximizing equipment performance and longevity. Modern drain cleaning machinery features advanced functions that require knowledgeable handling to ensure safe and efficient operations.
Prioritize Operator Training and Resources
Each piece of equipment comes with its own set of controls and guidelines. Make sure operators consult user manuals and participate in hands-on training sessions.
Ensure Proper Equipment Use
Even the best machines can underperform if misused. Follow the manufacturer’s guidelines for startup, operation, and shutdown to avoid undue strain and potential damage to essential components.
Reinforce Safety Protocols
High-pressure systems require strict safety measures. Operators should:
- Wear proper PPE, including gloves, goggles, and slip-resistant footwear.
- Verify that hoses and connections are securely fastened.
- Stay alert for unexpected changes in pressure or temperature.
Schedule Regular Refresher Training
Operator proficiency can diminish over time. Regular training updates help staff stay informed about new techniques, safety protocols, and best practices, enabling them to identify and address early signs of equipment issues.
Common Mistakes to Avoid When Maintaining Drain Cleaning Equipment
Municipalities frequently operate drain cleaning equipment under heavy daily use, which can stress key components. Even with a solid maintenance regimen, some pitfalls can undermine equipment reliability:
- Neglecting Scheduled Maintenance: Skipping routine tasks might offer temporary convenience but often leads to more severe damage over time.
- Using Improper Cleaning Tools or Products: Always use manufacturer-approved agents and tools to prevent corrosion or accelerated wear of critical parts.
- Mixing Genuine and Non-OEM Parts: While non-OEM parts may be less expensive, mismatched specifications can decrease performance and reduce lifespan.
- Ignoring Early Warning Signs: Abnormal noises, fluctuating pressure, or overheating should be addressed promptly to avoid costly failures.
- Overlooking Operator Practices: Even the best maintenance plan can falter if equipment is misused or standard procedures are ignored.
Proper maintenance of drain cleaning equipment is essential for ensuring its longevity, efficiency, and safety. By adhering to regular cleaning, lubrication, and inspection routines, you can significantly reduce the risk of unexpected breakdowns and costly repairs. Additionally, investing in operator training and choosing suitable parts can enhance performance. By keeping these practices in focus, facilities can maintain optimal operational standards and prevent disruptions.
Optimize Equipment Performance with Consistent Maintenance Practices
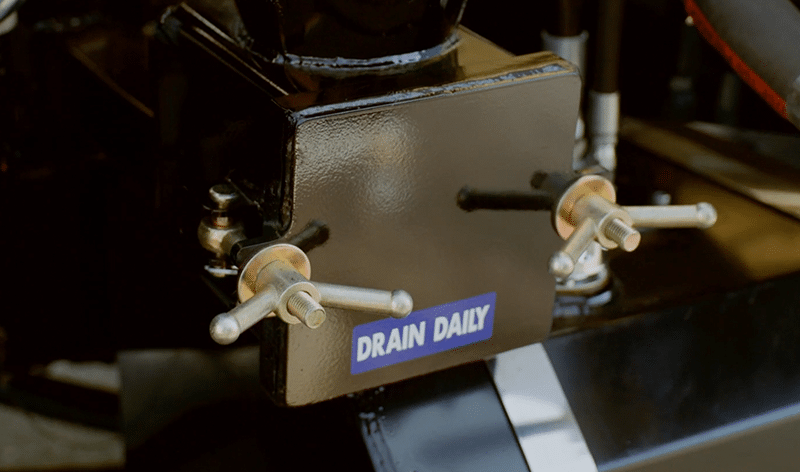
Adopting a proactive approach to equipment care—through routine inspections, timely repairs, and consistent operator training—ensures dependable drain cleaning performance. A comprehensive preventive maintenance plan that addresses small issues before they escalate will help reduce downtime, extend equipment lifespan, and optimize resource allocation.
At Brown Equipment, we appreciate the critical role that high-performing machinery plays in sewer and water management. With our vast inventory of equipment, specialized services, genuine parts inventory, and dedicated support, we provide comprehensive solutions designed to meet your operational needs.
Don’t let minor issues turn into major setbacks. Our commitment to relationship-driven support means you can achieve optimal performance from your drain cleaning equipment—today and for years to come. Contact a Brown Equipment equipment consultant today to learn more about our quality equipment and commitment to customer service.