For municipalities, contractors, and facility managers, capital-intensive equipment—such as sewer cleaning trucks, landscaping tools, and snow and ice management vehicles—is crucial for daily operations. When these machines begin to falter, the key question arises: “Is it more cost-effective to repair or replace?” This decision goes beyond immediate expenses, encompassing downtime, equipment lifecycle, compliance requirements, performance benchmarks, and long-term value. In industries such as sewer, water, and wastewater management and highway maintenance, making the wrong choice can lead to setbacks, missed deadlines, or disruptions in essential services. By thoroughly assessing factors such as cost, maintenance needs, compliance, and future value, organizations can maintain operational continuity while maximizing efficiency.
Key Considerations for Repairing or Replacing Equipment
Deciding between repairing or replacing equipment involves understanding how the decision affects reliability, productivity, and long-term value. Assessing aspects such as lifecycle, performance history, technological advances, and compliance requirements helps align choices with operational needs and strategic goals.
Evaluating Equipment Lifecycle and Usage
Every piece of heavy machinery reaches a point where the cost and frequency of repairs become unsustainable. Assess whether your equipment shows signs such as:
- Rising repair costs
- Difficulty sourcing replacement parts
- Inability to meet current performance demands
For example, sewer cleaning trucks often used intensively may experience faster wear and tear than seasonal vehicles. Evaluating these factors helps determine if repairs can extend the equipment’s life or if replacement is necessary.
Examining Frequency of Breakdowns and Maintenance History
A detailed maintenance history can reveal recurring issues and predict future performance. Frequent breakdowns and repeated repairs may signal that a machine is no longer reliable, leading to costly downtime and operational disruptions. Tracking repair records, parts replaced, and overall downtime can help decide if the issues are manageable or if replacement is the better option.
Considering Technological Advancements in New Models
Modern equipment often includes significant technological improvements that enhance performance, efficiency, and safety. For example, new sewer cleaning trucks may feature water recycling systems that reduce downtime, while next-generation snow management vehicles can optimize material application to lower operational costs. Although new equipment requires a larger initial investment, the long-term savings through improved efficiency and reduced maintenance effort can be substantial.
Addressing Compliance and Regulatory Requirements
Older equipment may struggle to meet updated standards, potentially incurring high costs for retrofitting. In industries with strict compliance requirements, such as sewer management and roadway maintenance, the expense of upgrading an aging machine may rival that of replacing it entirely. Newer models not only meet current regulations more easily but also position your organization as a leader in sustainability.
By evaluating these key considerations—lifecycle, performance history, technological updates, and compliance—you can determine whether repairing or replacing your equipment is the best choice for maintaining efficient operations.
Financial Analysis: Repair Costs vs. New Equipment Investment
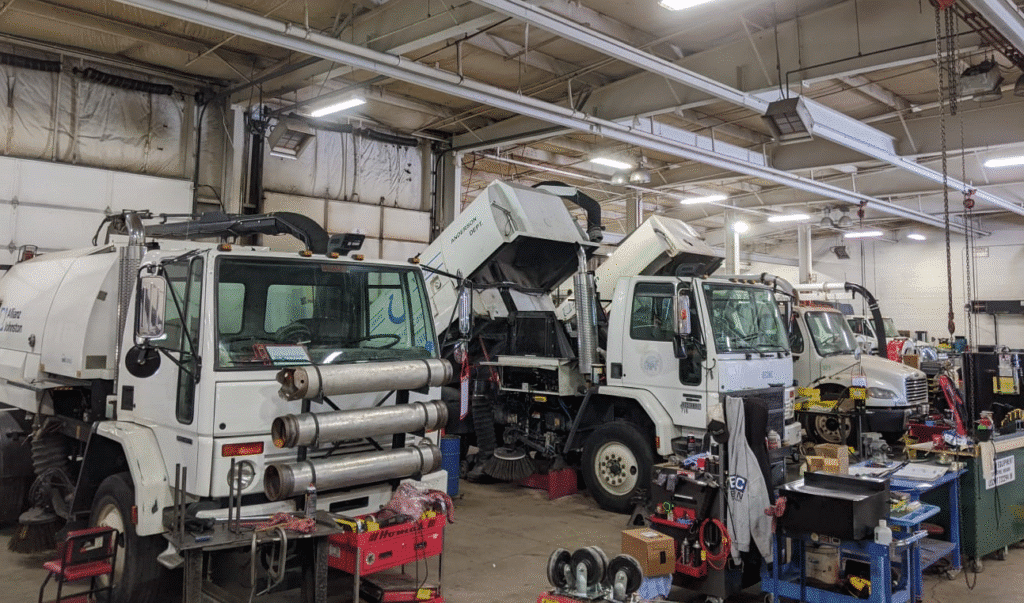
Conducting a thorough financial analysis is essential when weighing repair against replacement. While repairs might appear cheaper in the short run, the cumulative costs over time can outweigh the expense of new equipment.
Assessing the True Costs of Repairs
The cost of repairs includes not only parts and labor but also hidden expenses such as:
- Cumulative downtime
- Lost productivity
- Additional scheduling challenges
For example, a sewer cleaning truck that is frequently out of service during heavy storm periods can delay critical projects and lead to increased overtime or rental costs. Analyzing repair frequency, downtime, and the recurring nature of failures provides a clearer picture of whether ongoing repairs are financially viable.
Understanding the Value of New Equipment Investment
Investing in new equipment involves an upfront expense, but it brings long-term benefits. Evaluating the Total Cost of Ownership (TCO) is critical, including:
- Initial purchase price
- Lower maintenance costs due to warranties and modern engineering
- Operational savings from improved fuel efficiency and performance
- Residual value or trade-in potential at the end of its lifecycle
For example, a modern snow management vehicle with precise material application technology may reduce material usage and increase operational efficiency during peak periods. Such savings can balance the higher initial cost over time.
Weighing Long-Term Value
Over time, older machinery may depreciate rapidly, making frequent repairs less valuable compared to investing in reliable new equipment. Conducting a break-even analysis—comparing cumulative repair costs with the predictable expenses associated with new equipment—can clarify the point at which replacement becomes the more viable option.
By balancing repair costs, ownership expenses, and long-term value, decision-makers can adopt a strategy that supports both operational efficiency and fiscal responsibility.
Operational Impacts: Downtime and Efficiency
Evaluating the operational impacts of downtime and efficiency is critical when choosing between repairing and replacing equipment.
The High Cost of Downtime
Equipment downtime disrupts essential services, delays projects, and increases costs. For instance, a malfunctioning asphalt patcher during peak repair periods can force schedule adjustments, extra labor hours, and emergency rentals. Such disruptions not only affect budgets but can also harm public safety and customer satisfaction.
Productivity Gains with Modern Equipment
Upgrading to modern equipment can significantly boost productivity. Newer machines are often equipped with advanced features that allow faster, more precise operations with less downtime. For example, upgraded sewer cleaning trucks with integrated water recycling systems can reduce time lost on refills, enabling crews to complete more tasks efficiently and reliably.
Beyond Efficiency: Morale and Consistency
Reliable equipment minimizes disruptions and helps maintain workforce morale. Consistent performance ensures that teams can focus on quality work without the stress of unexpected breakdowns, thereby enhancing overall productivity and service delivery.
Industry-Specific Examples for Decision-Making
The decision to repair or replace equipment varies by industry and its unique challenges. Here are key examples:
Sewer, Water, and Wastewater Management
Malfunctioning sewer cleaning trucks can lead to project delays and safety hazards. An aging vacuum truck that frequently breaks down may result in increased maintenance costs and service disruptions. Upgrading to modern models with water recycling systems not only improves efficiency but also reduces water consumption and meets regulatory standards more easily.
Roadway and Highway Maintenance
During high-demand periods like winter, reliable roadway maintenance equipment is vital. Vehicles such as snow management machines that frequently require repairs can disrupt public safety efforts. Replacing outdated equipment with models featuring real-time monitoring and efficient fuel systems can minimize downtime and improve overall reliability.
Landscaping and Vegetation Management
Efficient landscaping equipment is especially important in challenging environments. For example, when older mowers or land clearing equipment result in slower project completion or pose safety risks, modernizing with equipment that offers enhanced safety features and greater maneuverability can greatly boost productivity.
The Role of Preventative Maintenance and Custom Solutions
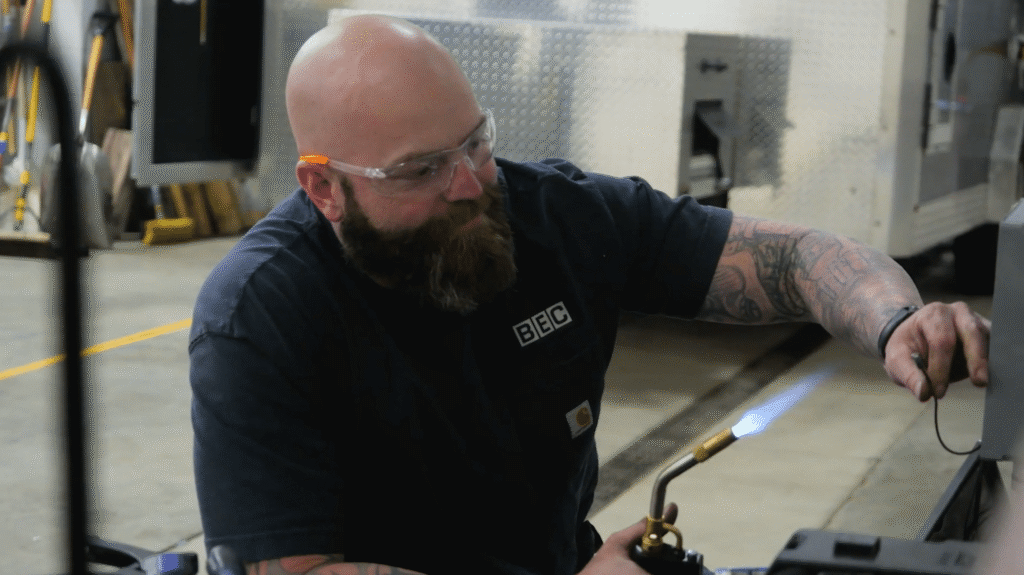
Preventative maintenance and custom solutions are practical ways to extend equipment life and enhance performance without immediate replacement.
The Importance of Preventative Maintenance
A robust preventative maintenance plan addresses minor issues before they escalate, reducing unexpected breakdowns and extending useful life. Regular inspections, timely lubrication, and part replacements help maintain peak performance and avoid costly repairs.
Custom Solutions: Enhancing Performance Without Replacement
When full replacement isn’t necessary, custom modifications or reconditioning can revitalize aging equipment. Rebuilding key components or upgrading critical features can restore functionality and improve efficiency, often providing a cost-effective alternative to complete replacement.
Choosing OEM Parts for Longevity
Using Original Equipment Manufacturer parts ensures that repairs meet the highest standards, enhancing the durability and reliability of your machinery. This approach not only improves performance but also helps maintain equipment value over time. For example, using quality OEM parts can be crucial to ensuring long-term reliability.
Factors Beyond Cost: Strategic and Operational Considerations
Deciding between repair and replacement involves strategic considerations that go beyond mere financial calculations.
Reliability as the Cornerstone
Frequent breakdowns disrupt operations and erode productivity. Reliable equipment minimizes downtime and provides operational stability, enabling better planning and consistent service delivery.
Advancing Sustainability
Upgrading to eco-friendly machinery helps meet compliance requirements and reduces environmental impact. Newer models often feature low-emission engines and advanced technologies that support long-term sustainability, aligning operational practices with environmental standards. This commitment to sustainability not only meets regulatory demands but also furthers community and environmental goals.
Building Resilience
Modern equipment offers enhanced flexibility and adaptability, preparing your organization to meet future demands. Investing in advanced machinery can reduce risks during high-demand periods or emergencies, ultimately bolstering operational resilience.
Expert Assessment: A Vital Step in the Decision-Making Process
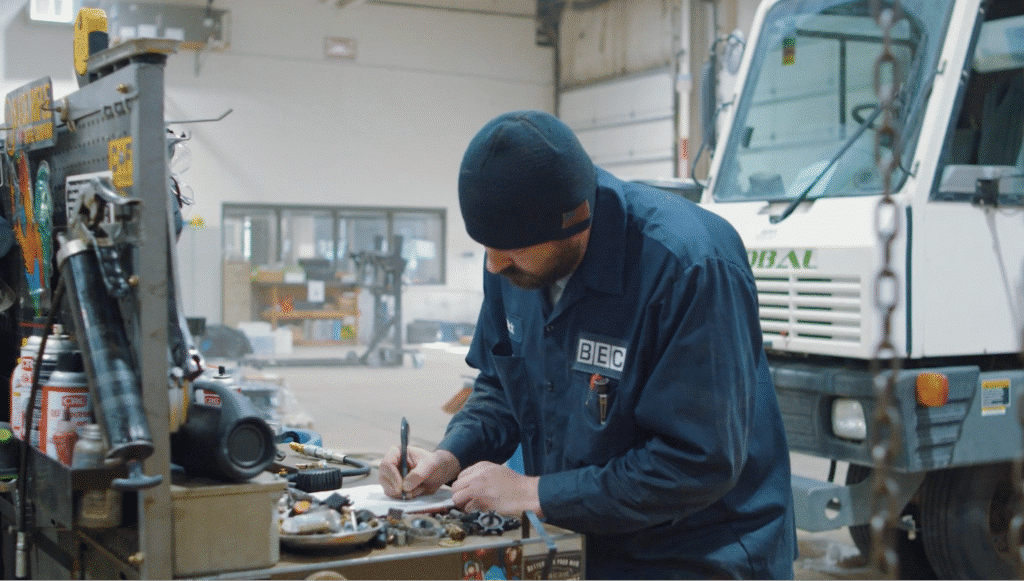
Enlisting industry professionals for an expert assessment is key to making an informed decision. Expert evaluations consider:
- Detailed maintenance records and performance trends
- Market trends and costs for both repairs and new equipment
- Feasibility of upgrades versus full replacement
- Mechanical and structural integrity evaluations
An objective, data-driven assessment helps clarify whether repairs can restore functionality or if the equipment is nearing the end of its lifecycle. Relying on expert guidance minimizes risks and supports a choice that aligns with financial and operational needs.
Future Trends in Equipment Management
Looking ahead, emerging technologies continue to influence how organizations approach repair versus replacement. Innovations such as the integration of Internet of Things (IoT) sensors and advanced analytics are setting new standards in equipment management. These tools provide detailed insights into machine performance, predicting failures before they occur and allowing for proactive maintenance. Ongoing technological developments also drive improvements in efficiency and safety, making it easier for organizations to accomplish tasks faster and with fewer interruptions.
By staying informed about these emerging technologies, decision-makers can schedule proactive maintenance, reduce operating expenses, and plan equipment upgrades more effectively. Organizations that integrate such innovations are often better positioned to maintain continuous service, respond to unexpected disruptions, and align their operations with evolving regulatory standards.
Recommendations for Future Best Practices
It is advisable for organizations to establish continuous training programs and adopt advanced monitoring systems. This proactive approach empowers teams to address emerging issues and ensures clear communication when managing repairs and replacements, ultimately supporting optimal long-term performance.
These best practices align well with Brown Equipment Company’s emphasis on after-sales support and training, which can significantly extend equipment longevity. By combining systematic preventative maintenance, modern technological tools, and professional guidance, your organization can minimize downtime and enhance operational success.
Watch the video below to get a behind-the-scenes look at what it really means to be a Brown Equipment Company Service Technician. From showing up with purpose to putting the customer first, our techs don’t just repair—they represent our BEC Blue Values every step of the way.
Leveraging Data-Driven Insights for Improved Equipment Decisions
Making well-informed choices about ongoing repairs or replacements requires clear data on machinery usage, performance trends, and maintenance patterns. Collecting and analyzing operational data—such as fuel consumption rates, hourly usage logs, and service records—allows teams to pinpoint inefficiencies and schedule repairs proactively. By reviewing these data points diligently, decision-makers gain a holistic understanding of the factors that contribute to equipment failures or declining performance. Over time, these insights enable more accurate forecasting of when to upgrade machines, how to budget for future acquisitions, and where to focus preventative maintenance efforts to extend equipment lifecycles. Furthermore, leveraging data analytics helps detect patterns, empowering organizations to enhance productivity, reduce operating costs, and allocate resources more strategically.
Need Help Deciding if You Should Repair or Replace?
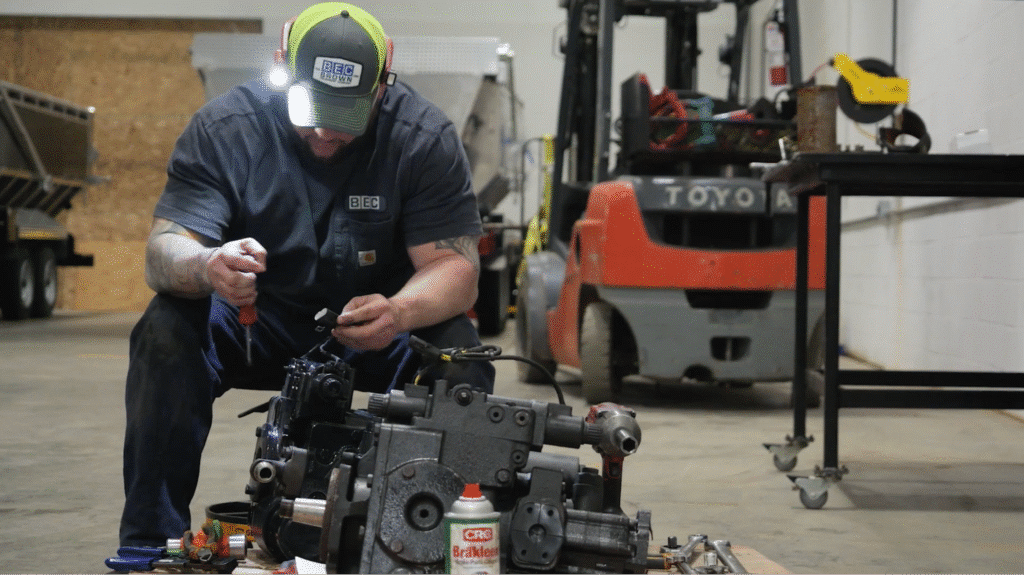
Deciding whether to repair or replace critical equipment is a complex process with long-term implications. Repairs may extend the life of existing machinery at a lower immediate cost, but new equipment can offer enhanced technology, efficiency, and reliability while meeting regulatory standards. A strategic approach—evaluating equipment condition, financial implications, operational impacts, and expert insights—ensures that your decision maximizes efficiency and reduces risks.
At Brown Equipment Company, our tailored assessments and industry expertise help guide you toward solutions that optimize performance and support long-term success. Contact Brown Equipment Company today to take the next step in ensuring your operations remain resilient and efficient, backed by expert advice and innovative technology.