Imagine a world where pipeline failures are rare, where leaks and corrosion are caught early—before they escalate into costly disruptions. Pipeline infrastructure is the backbone of modern communities, and its safety is paramount for municipalities, large contractors, and facility managers. Advanced non-destructive testing (NDT) methods now enable fast, safe, and cost-effective inspections without interrupting operations.
This article offers an accessible overview of the most effective NDT techniques, explains their benefits with clear, straightforward language, and shows how these innovations are securing the future of essential pipeline systems.
Non-destructive testing detects defects without altering or damaging pipelines. By identifying issues early, NDT prevents minor problems from growing into major failures while promoting safety, reliability, and sustainability. Combining traditional methods with modern technology now provides inspections that are both comprehensive and easy to understand.
The Importance of Pipeline Integrity and Common Challenges
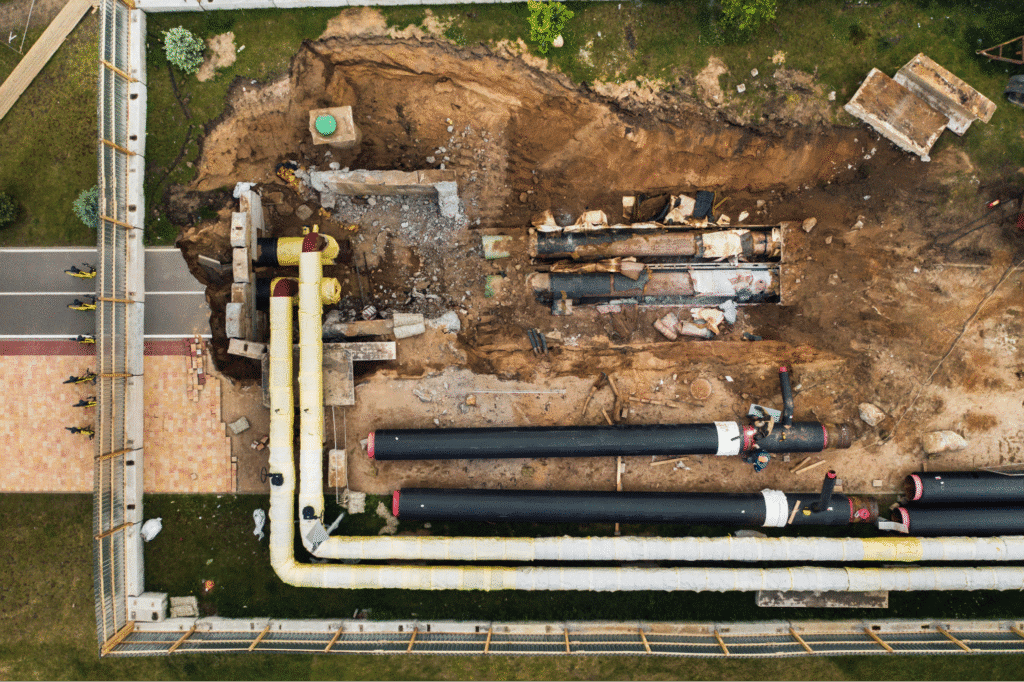
Ensuring the integrity of pipelines is crucial for maintaining reliable service, safeguarding the environment, and protecting public safety. Proper pipeline maintenance not only extends the operational lifespan of the infrastructure but also prevents potential hazards associated with leaks, corrosion, or blockages. However, maintaining this integrity comes with its own set of challenges:
- Corrosion: Over time, exposure to chemicals and harsh environmental conditions can deteriorate pipeline materials. This gradual weakening necessitates continuous protective measures and vigilant monitoring to prevent failures.
- Leaks: Even minor leaks can lead to significant resource loss, environmental harm, and safety issues. Early detection is key to mitigating these risks and ensuring efficient pipeline operations.
- Blockages: Accumulations of sediment or biological growth can impede flow within the pipeline, resulting in operational inefficiencies and increased pressure on the system.
- Aging Infrastructure: Many pipelines are decades old and require enhanced maintenance and potential upgrades to meet current safety and performance requirements.
- External Damage: Pipelines are susceptible to damage from construction work, natural disasters, or accidents, which can compromise their safety and functionality.
Regulatory guidelines, such as those outlined by the PHMSA Pipeline Safety Regulations, emphasize the necessity of consistent, comprehensive assessments to effectively address these vulnerabilities. A proactive approach employing non-destructive testing (NDT) methods helps identify problems early, ensuring that pipelines remain safe, efficient, and in compliance with safety standards.
Why Non-Destructive Testing Methods Matter
In the world of pipeline inspections, non-destructive testing (NDT) methods stand out due to their ability to evaluate the integrity of pipelines without causing damage. As infrastructure ages and regulatory requirements become more stringent, the demand for efficient and reliable inspection processes grows. NDT methods offer unparalleled advantages, allowing for thorough assessments that help maintain operational efficiency, safety, and compliance with standard protocols. Here’s why these methods are indispensable:
- Minimal Downtime: NDT enables comprehensive inspections without the need for shutdowns, keeping pipeline operations uninterrupted and efficient.
- Enhanced Safety: By adopting non-intrusive techniques, these methods greatly reduce potential hazards, ensuring the safety of both inspection personnel and the environment.
- Early Detection: Utilizing advanced precision instruments, NDT methods can identify defects and irregularities early on, preventing minor issues from escalating into significant, costly problems.
- Extended Lifespan: Regular inspections through NDT facilitate targeted maintenance, contributing to the prolonged functionality and service life of pipeline systems.
- Regulatory Compliance: NDT provides detailed and accurate reporting, assisting pipeline operators in meeting rigorous safety and regulatory standards with ease.
- Cost-Effectiveness: By preventing serious defects and reducing the likelihood of extensive repairs, these methods save money and resources in the long term.
NDT methods play a critical role in securing the integrity and reliability of pipeline systems. By offering a comprehensive toolkit for non-invasive inspection, they ensure that infrastructure can meet current demands while supporting sustainable growth. As pipelines continue to serve as vital conduits for resources around the globe, employing robust NDT techniques guarantees safety, efficiency, and compliance—cornerstones of any successful pipeline management strategy.
Non-Destructive Testing Methods for Pipeline Inspection
There are various non-destructive testing methods available for pipeline inspections, each with its own specific benefits and applications. By understanding these methods and their advantages, operators can select the most suitable technique for their pipeline’s unique needs, ensuring thorough and effective inspections.
Ultrasonic Testing (UT)
Ultrasonic testing details use high-frequency sound waves to examine pipelines for internal defects such as cracks or corrosion. In this process, a device called a transducer transmits sound waves into the pipeline. When these waves encounter an abnormality, they bounce back, allowing inspectors to locate and size the defect quickly.
Key advantages include:
- Versatility: Effective on a variety of materials like metals, plastics, and even concrete.
- Instant Data: Provides immediate, real-time measurements for rapid decision-making.
- Portability: Available in handheld units for remote inspections or integrated into automated systems for continuous monitoring.
This non-invasive approach is particularly useful for sewer and water pipelines, allowing targeted repairs while keeping services operational.
Magnetic Particle Testing (MPT)
With ultrasonic testing providing a clear view inside pipelines, another method excels at exposing surface-level issues. Magnetic particle testing detects surface or near-surface flaws in ferromagnetic materials, such as steel. The process begins by magnetizing the pipeline, then applying fine magnetic particles that cluster around imperfections—like cracks or weak welds—making them visible to inspectors.
Benefits include:
- Quick and Simple: Uses basic equipment to deliver rapid surface assessments.
- High Sensitivity: Detects even small cracks or initial signs of corrosion.
- Cost-Effective: An economical option ideal for routine inspections.
By reliably identifying surface flaws early, MPT helps ensure that minor defects are remedied before they escalate.
Radiographic Testing (RT)
Whereas magnetic particle testing focuses on surface issues, radiographic testing uses X-rays or gamma rays to generate detailed images of a pipeline’s internal makeup—akin to how medical X-rays reveal problems inside the human body. This method uncovers hidden defects such as voids, internal corrosion, or cracks in welds. Because radiographic testing employs ionizing radiation, inspectors follow strict safety protocols.
Distinct advantages include:
- Detailed Imaging: High-resolution visuals capture subsurface flaws that might go undetected.
- Accurate Weld Assessment: Essential for checking the quality of pipeline joints.
- Broad Applicability: Suitable for both new pipelines and aging infrastructure.
RT offers a comprehensive view of a pipeline’s condition, making it an essential tool for long-term maintenance planning.
Visual Inspection with Advanced Camera Systems
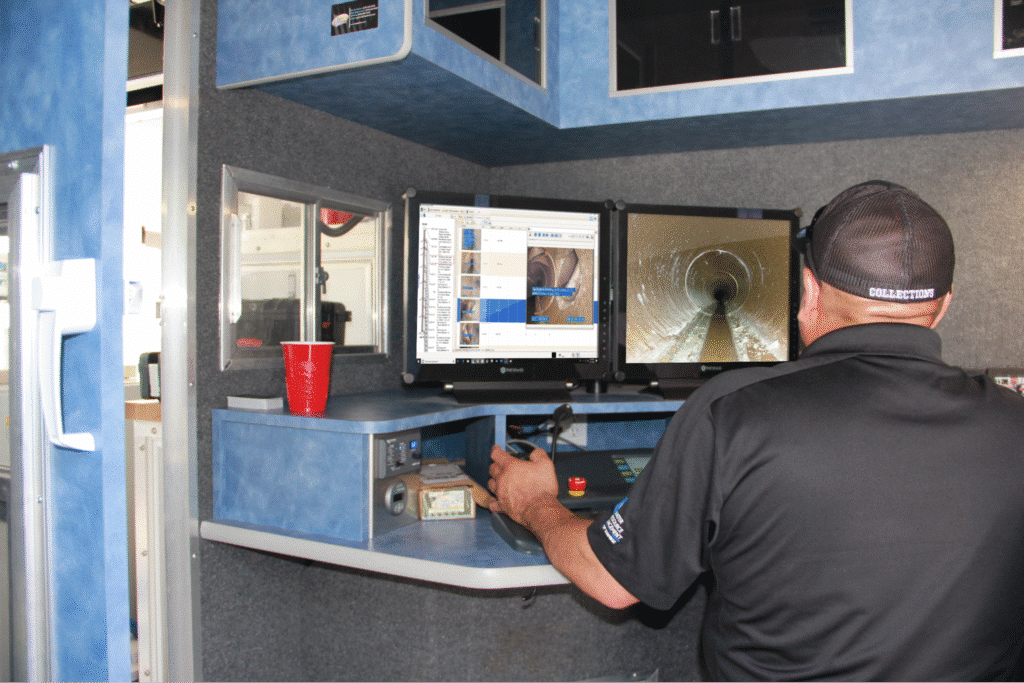
Beyond these imaging techniques, modern visual inspection methods provide a highly accessible means of assessing pipeline conditions in real time. Advanced pipeline inspection cameras have redefined visual inspections. Mounted on portable platforms or robotic units, these cameras provide a non-invasive way to inspect the interior of pipelines, even in hard-to-reach areas.
This technology offers several clear benefits:
- Immediate Clarity: Real-time, high-quality visuals help quickly locate surface defects and obstructions.
- Flexibility: Suitable for inspecting pipelines of various sizes, from small laterals to large mainlines and manholes.
- Data Analysis: Integrated software generates detailed condition reports to guide maintenance decisions.
Advanced camera systems give inspectors a comprehensive visual survey, enhancing proactive maintenance strategies and reducing the need for disruptive interventions.
Hydrostatic Testing
Complementing these electronic and visual methods, hydrostatic testing in pipelines involves filling the pipeline with a pressurized fluid and monitoring pressure levels to check for leaks or drops. By simulating daily operating conditions, this method determines whether the pipeline can withstand its intended working pressures.
Key features include:
- Effective Leak Identification: Controlled pressure tests expose hidden leaks or weak points.
- Structural Verification: Confirms that the pipeline retains its integrity under expected operating conditions.
- Complementary Confirmation: Often used alongside other NDT methods to verify overall performance.
While hydrostatic testing can require a temporary shutdown, it provides indispensable insights ensuring pipelines meet both regulatory and operational standards.
Which Non-Destructive Testing Method is Best for My Application?
Selecting the right NDT methods depends on the pipeline’s material, age, and operational requirements. For example:
- New composite pipelines may benefit from a mix of ultrasonic and radiographic testing during commissioning to ensure optimal integrity.
- Older steel pipelines might need frequent magnetic particle testing, combined with periodic visual inspections and hydrostatic tests for comprehensive evaluation.
- Oil and gas lines governed by the ASME B31.8 Code for Gas Pipelines also benefit from these rigorous NDT approaches.
Tailoring techniques to address specific vulnerabilities maximizes safety and efficiency.
Future Trends and Regulatory Implications
The future of NDT will likely see tighter integration with infrastructure operations, as regulations become more stringent to protect the environment and public welfare. Digital integration and advanced sensor arrays promise to further streamline testing processes. As sustainability continues to gain importance, adopting innovative NDT methods helps assure compliance while safeguarding infrastructure for the long term.
Emerging Technologies in NDT
Innovative solutions continue to refine NDT capabilities:
- Artificial Intelligence in NDT and machine learning streamline flaw detection and data analysis.
- Robotic Inspection Trends feature advanced sensors to traverse hazardous or complex sections of pipeline.
- IoT for Pipeline Monitoring employs real-time networks to gather data on pressure, temperature, and flow.
- Digital Twin Technology merges real-time NDT data with a virtual pipeline model. Operators can visualize pipeline health, simulate interactions, and pinpoint potential risks. Digital twins support prioritized repairs, fewer unscheduled outages, and lower maintenance expenses over the long term.
These advancements enhance detection accuracy and enable proactive, predictive maintenance that addresses issues before they become critical.
Strategic Considerations for Future NDT Deployment
When planning next-generation NDT initiatives:
- Assess Current Assets: Review pipeline conditions to steer testing strategies.
- Customize Inspections: Focus on hotspots to manage risks effectively.
- Foster Collaboration: Involve engineering, operations, and IT teams in designing integrated maintenance programs.
This balanced approach heightens operational efficiency, reduces management risks, and aligns with stringent regulatory requirements.
Overcoming Challenges in NDT Implementation and Integration
Although the benefits of NDT are clear, adoption can pose challenges:
- Data Integration: Combining multiple tests into a unified view requires specialized software.
- Financial Constraints: Investing in advanced equipment and training may be considerable initially.
- Skill Gaps: Mastering new technologies demands ongoing professional development.
A phased roll-out, guided by collaboration between equipment providers, operators, and data analysts, helps organizations realize the full value of NDT and encourages a proactive safety culture.
Industry Applications and Real-World Benefits
Real-life uses for NDT include:
- Routine inspections that maintain operational integrity.
- Emergency evaluations that minimize downtime after unforeseen incidents.
- Post-repair verification assuring that critical fixes will last.
By integrating NDT tools with proper asset management, pipeline operators achieve lower repair costs, bolstered reliability, and improved safety overall. These outcomes highlight the vital role of modern NDT methods in preserving essential sewer, water, and wastewater infrastructure.
Enhancing Sustainability and Efficiency Through NDT
Early detection of pipeline problems through NDT fosters targeted maintenance that diminishes waste and lowers environmental impact. Key sustainability benefits include:
- Reduced Waste: Targeted repairs curb unnecessary excavation and resource use.
- Lower Carbon Footprint: Fewer large-scale projects equate to reduced emissions and less community disruption.
- Extended Lifespan: Proactive upkeep prolongs pipeline operations, offering both financial and environmental rewards.
Selecting and Implementing the Right Tools for NDT Success
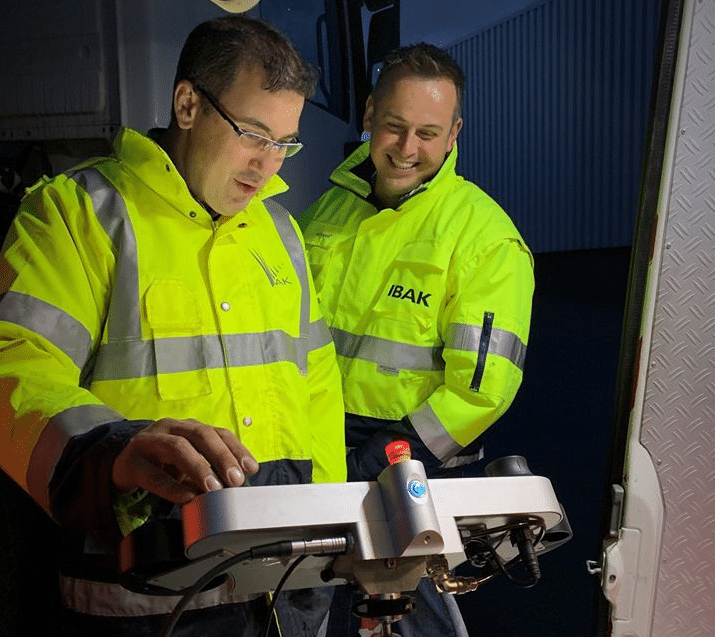
Building a robust NDT program begins with smart tool selection:
- Compatibility: Equipment must suit each pipeline’s specifications.
- Operator Expertise: Dedicated technical training unlocks the full power of inspection tools.
- Scalability: Solutions should grow with the organization’s needs.
- Reliable Support: Partner with trusted providers that offer ongoing assistance and custom solutions.
By focusing on these considerations, municipalities and contractors can create a dependable NDT framework that improves safety and efficiency. Furthermore, consistent collaboration with experienced vendors helps teams keep pace with technological developments, ensuring pipelines remain structurally sound and regulatory-compliant.
Long-Term Maintenance and Investment Considerations
A sustainable NDT program requires continuous technological upgrades and training. While initial outlays may be significant, benefits include reduced downtime, heightened safety, and better system performance overall. By embedding cutting-edge NDT methods into routine maintenance and monitoring, pipeline operators remain adaptable to evolving risks and requirements. In many cases, teams that prioritize advanced NDT technologies see fewer emergency repairs and significant cost savings over time.
Organizations responsible for municipal wastewater systems also benefit from these forward-thinking approaches. By leveraging NDT insights, they can prevent backups, avoid environmental hazards, and maintain essential public services without lengthy disruptions. As new materials and technologies emerge, a proactive attitude toward pipeline inspection ensures these systems operate reliably well into the future.
The Future of Pipeline Integrity with NDT Techniques
Advanced non-destructive testing methods are transforming pipeline inspections by offering precise, efficient, and safe assessments without halting crucial services. Techniques such as ultrasonic, magnetic particle, radiographic, and state-of-the-art camera inspections—assisted by hydrostatic tests—provide a thorough understanding of pipeline health. Emerging innovations, including artificial intelligence, robotic inspection, IoT-enabled sensors, and digital twin technology, drive predictive maintenance and proactive management strategies.
For municipalities, large contractors, and facility managers, adopting a robust NDT program is pivotal for enhancing safety, sustainability, and overall operational excellence. Reach out to Brown Equipment Company today to explore how our pipeline inspection and monitoring equipment solutions, expert guidance, and camera repair services can help you safeguard your infrastructure’s future.